March 5th 2025 10:26:27 AM
4 Inventory Management Tips to Help Your Company Ride Out the Rest of the Pandemic
January 4th 2022 11:00:00 AM
It’s a New Year and a new start on the calendar. We were all hoping the pandemic would be in our collective rearview mirrors by now. Unfortunately, we are still feeling the effects of COVID-19 in our homes and businesses. Since there are no clear answers about when the pandemic will end, we are left to continue making the best possible decisions, including ones about inventory management, in these uncertain times.
Managing Inventory Challenges in All Circumstances
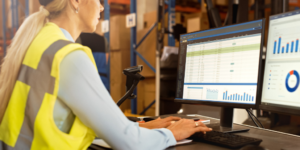
Ensuring that product levels are optimized can be challenging in the best business circumstances. All it would take to put things out of balance is for an expected shipment to arrive late or a retailer to get an unexpected run on a particular product. The company would have to make alternate plans quickly to deal with these unforeseen changes.
Many companies learned that disruption to their supply chain could cause havoc to even the best inventory management strategies. Toilet paper and personal protective equipment (PPE) suppliers had difficulty keeping up with demand at the pandemic’s start. (In the former case, consumers also did significant hoarding.) In 2021, several types of products, such as lumber, takeout containers, and poultry were difficult to acquire at some point.
Companies Forced to Rethink Inventory Management
These supply chain interruptions and challenges in obtaining needed products forced many companies to rethink their inventory management approach.
- Many of them found that taking a lean approach was not working for them.
- They were also dealing with continuing labor shortage issues.
- Companies still using clipboards and spreadsheets to manage inventory discovered that these low-tech tools were not the best way to track products in the warehouse.
Four Inventory Management Tips
The beginning of the year is a great time to take stock of your business and make some positive changes where needed. The good news is that your company has made it through the pandemic this far. With some flexibility and innovative thinking, you can be on your way to weathering whatever is to come.
1. Take a good look at your current inventory management practices.
You can’t make good decisions about what might need to change in your inventory management policies until you take an honest look at where you are right now. Figure out what is working well and where you could make some improvements. When doing this internal review of your inventory management policies, consider points such as:
- Does your business have the right level of automation in its inventory management processes?
- Are you using the right software for your company’s needs?
- What data is needed to make ongoing inventory management decisions?
- What steps can we take to reduce costs while maintaining appropriate inventory levels?
2. Give yourself a bit of a buffer in your inventory planning.
The “just-in-time” (JIT) approach to inventory planning has its place. It can be highly effective as long as your supply chain is reliable. JIT may be too risky for your company in these uncertain times, and too many variables are involved.
Expect delays and place your orders accordingly until the supply chain returns to what your business considers “normal” or pre-pandemic performance levels.
3. Automate your inventory management system.
The labor shortage in the warehouse industry is an ongoing issue that is not close to a resolution. Since hiring more workers is not feasible, relying on warehouse management systems to handle activity within your facility is a reasonable step.
When you take this step, you can get and maintain control over your inventory, and it is much less likely that products will become lost or misplaced. At this time, maintaining accurate records is crucial and automating your processes allows your team to stay on top of current stock.
4. Plan now for shortages and interruptions in your supply chain.
Don’t wait for the proverbial other shoe to drop before you make plans. Use “What if?” scenarios. Think about and plan for what you could do if your regular supplier could not deliver the inventory you have ordered on time.
- Have a list of backup suppliers on hand that can be ready to step in on short notice.
- If you cannot fill orders in your usual time frame, reach out to customers to communicate the news.
- Have a plan for letting new customers know about delays in fulfilling orders before they buy. This step helps you manage your customers’ expectations before they become an issue.
Scanco Sage 100 Warehouse Automation Fits Your Business Needs
Whether you’re operating a small, mid-size, or large operation, you can count on Scanco’s warehouse management systems to fit your requirements. All our options integrate seamlessly with Sage 100. They are easy for your team to learn and use.
- Scanco WMS Essentials is the best choice for small businesses and companies introducing automation to their workforce. This product automates your inventory cycle counting, meaning you can throw away the clipboard forever! Your team members have multiple hardware accessory options for scanning barcodes and looking up items. Counts are sent in real-time automatically into Sage 100.
- Scanco WMS Advanced gives you all the features of WMS Essentials. This option is packed with advanced features, such as MultiBin Functionality, Physical Count by Bin, Alias Item Creation, Pack List Printing, Directed Order Picking, Directed Replenishment, and more.
- Scanco WMS Professional includes all the features of WMS Essentials and WMS Advanced. This option for enterprise-level companies gives you Directed Putaway, Wave Picking, and Directed Shipping. You can also take advantage of unlimited customer support when choosing WMS Professional.
Would you like to learn more about Scanco Sage 100 Warehouse Automation solutions for your business? Contact us today to discuss your options with one of our solutions experts.