March 5th 2025 10:26:27 AM
Barcoding Gives You Better Inventory Control
September 20th 2022 11:00:00 AM
Companies are always looking for ways to stay competitive by decreasing costs to increase profits. It can be tempting to consider other methods of reducing costs, such as keeping hiring down or reducing the advertising or marketing budgets. Unfortunately, these solutions can end up harming the company.
Inventory control is not something that immediately comes to mind when considering ways to keep costs in check. One way to improve inventory control is by introducing a sound barcoding system.
Custom Barcoding System Conveys a Multitude of Information
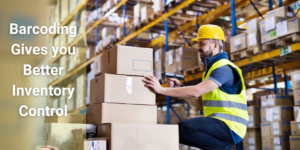
Barcoding software allows a company to set up its items in the computer system in the manner that makes the most sense. The printer produces the custom barcode that conveys the information required to track inventory. There is no need to use paper and pencil to make a note each time an item is received, relocated, or sold to a customer.
A barcode can tell the warehouse team several things about an item if set up correctly:
- Age
- Color
- Location in the warehouse
- Quantity
- Size
- Weight
The barcode is customizable (up to the system’s limits) to provide as much detailed information about the inventory as the company requires for tracking.
Benefits of Barcoding for Inventory Control
Introducing barcode scanning to your warehouse gives your team several advantages, including the following:
- Less chance of human error
Using barcodes to process data is much more accurate than having a data entry operator perform this function manually. Humans are intelligent and can perform many tasks well, which doesn’t mean we are flawless. Anyone who uses a keyboard makes typos.
Barcode scanners reduce training costs for new staff. The new team member points their hardware device toward the barcode and clicks.
- Immediately available data
Suppose you have your inventory data entered into your computer system manually. In that case, there is always a gap between your records and what is on hand in the warehouse. Barcode scanners immediately upload their results into your system; the data is always up to date and accurate.
Your procurement team always knows what is in stock when placing orders.
Your sales team can check to confirm that items are available for customers—and close more deals.
- Better inventory control
Barcode scanningtracks your inventory much more accurately than physical counts. This method also makes calculating inventory turnover rates a much easier process. Once you have a better handle on your inventory turnover, you can hold less inventory in stock and lower your carrying costs.
- Economical to implement
Barcoding is a low-cost system to implement for your business. You’ll be able to start generating your custom barcodes immediately after installation. Apply the barcodes to your stock, and you can begin tracking your inventory and your savings.
- More precise decision making
Managers who have access to more accurate data with barcoding make better decisions. Forecasting demand is more precise when the data is up to date. Budgeting for the company is more accurate when inventory and sales figures are exact.
How to Keep Your Inventory Counts in Check After You Choose Barcoding
The following tips will help keep your inventory counts accurate once your barcoding system “goes live.”
- All inventory must have a barcode label.
- All inventory received must be scanned before being put away.
- An employee scans all stock before shipping or moving inventory to a new location in the warehouse.
- Conduct spot checks on your inventory regularly. Compare it with written reports to confirm what is in bins or shelves.
- Analyze inventory reports routinely. This practice will guard against overstocks and help ensure you have adequate levels of each item available.
Improved Inventory Control Saves Money
How does improved inventory control help improve your bottom line? Here are a few examples:
- It frees up your cash by reducing or eliminating slow-moving stock.
- It assists in identifying items that are in high demand so you can order sufficient quantities of these products.
- Your company will avoid inventory mistakes due to human error in manual entry.
- There will be fewer stock-outs, which means your company saves on rush shipping charges to keep orders filled.
- Your sales and customer service teams always know what is on hand in the warehouse, leading to improved customer support.
DashPrint Makes Barcoding Easy and Convenient
DashPrint connects to your Sage ERP database and makes all your barcode labeling activities easy. Everything takes place conveniently from your Scanco Dashboard, and you don’t need a separate program to run your barcode labels. Automating your receiving, putaways, and inventory is a streamlined process your team can learn quickly.
Printing labels is no problem when you choose DashPrint. Your team members can preview any label before printing to look for errors.
The software comes with 33 Label Matrix design file templates that you can format to any printer brand or model.
You also receive 33 Zebra design file templates that you can use “out of the box” or make quick edits on before use.
With DashPrint, all your barcode labels will be consistent. A team member uses the Tab key to move between fields on the label. Once the team member completes the label, they can send it to print to a local printer, a networked printer, or a printer in a remote location.
DashPrint has multiple setup options, so you can customize it to suit your company’s specific needs.
Scanco SkyPrint Takes Warehouse Barcoding Mobile
SkyPrint is available within Scanco Warehouse. This option makes barcoding warehouse labels easy. Your team can print labels by clicking a button (no manual entry required) and send them to multiple printers. Auto-populating shipping, receiving, and inventory labels is an easy process. Do you need customized designs for each user? SkyPrint does that too.
Do you have questions about DashPrint or SkyPrint and barcoding for your warehouse operation? Contact us online or call (330) 645-9959 to make an appointment with a Scanco Solutions Expert today.