March 5th 2025 10:26:27 AM
How to Achieve Supply Chain Resilience in the Post-Covid World
June 20th 2023 11:00:00 AM
Before Covid-19 became a household word and everyone became tired of the regular news broadcasts reminding all of us about its impact on our daily lives, supply chains operated in the background. Much like the plumbing in a company’s building, as long as it was working properly, no one had much reason to think about it. Now, the plumbing of today’s business is front and center. Supply chain resilience is now on everyone’s radar, which isn’t exactly a positive sign.
Covid-19 Only One Factor Impacting Supply Chains
The World Health Organization (WHO) has officially declared that the global pandemic is over. It felt at times as though it was going to drag on forever. Covid-19 was definitely a significant factor which impacted the global supply chain. In the post-pandemic world, the Ukraine conflict also plays a role. This conflict has directly led to higher food and fuel costs, along with difficulty in supplying semiconductors and fertilizer to consumers. Delays at international ports, labor shortages, and extreme weather have only added to supply chain issues.
Supply Chain Resilience Post-Covid
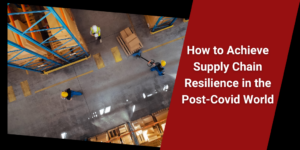
A resilient supply chain can respond to unexpected events without interrupting the supply to customers. Adding extra stock to inventories is part of supply chain resilience but it isn’t the entire story. There are other strategies that can be used to mitigate supply chain risk and deal with future disruptions.
1. Remember Your Employees are Your Best Resource
Without your employees, your business (and your supply chain) wouldn’t run. It’s that simple.
In the post-Covid world, build resilience into your supply chain by investing in your employees. Offer training through various media, such as videos, lunch-and-learn sessions, and programs offered by third-party providers. These types of programs are usually seen as something that falls under the umbrella of the Human Resources Department. However, they are crucial to business operations.
Ideally, supply chain employee teams should feel comfortable moving between tasks as the company’s needs change. They should receive training in advanced technologies (and refresher training as needed).
The benefit to employees is that they remain interested and are more engaged in their work. Employers benefit because these workers are more productive, work harder, and are less likely to leave the company for other opportunities.
2. Move from a Global to a Regional Logistics Hub
The modern supply chain network has been optimized to find the supplier who can produce the required items with the shortest lead times at the best possible price. From a manufacturer’s point of view, electronics made in China have generally fit those requirements. However, the pandemic has revealed that sourcing from suppliers in one geographic location has its inherent risks.
Instead of relying on global suppliers, now is the time to switch to suppliers at a regional level. Eliminate dependencies on a single source for inventory, raw materials, parts, etc. Instead, establish a flexible supply chain which includes suppliers who will source and provide the needed products from their own backyards.
3. Invest in Technology for Supply Chain Visibility
The challenges businesses have faced during the pandemic have made it clear that supply chain disruptions are often caused by several events instead of one main trigger. Factory shutdowns, weather events, and materials shortages have all been contributing factors to the supply chain disruptions that businesses still encounter.
Visibility is crucial for companies wishing to manage their supply chains. Technology can increase visibility and assist management in planning for different possible scenarios. The planning should include the following steps:
- Lay out your company’s supply chain.
- Rank your suppliers as Levels 1, 2, and 3.
- Put systems in place so that your supply chain team understands where each supplier ranks throughout the supply chain.
When an issue comes up that may lead to a disruption, your supply chain team already has a list of suppliers in hand. They know who to call on to step in to minimize the impact on the supply chain.
Scanco Production Management Plus Gives You Process Visibility
Scanco Production Management Plus is integrated with Sage 100 and is ideal for made-to-order manufacturers or distributors moving less than 10,000 orders daily. This module keeps organizations aware of the status of their items, their costs, and the material quantities needed to fill orders. The result is higher visibility, greater accuracy, and more optimized inventory.
Real Time Visibility. Your supply chain teamcanaccess up-to-date progress reports to determine where you are in the supply process. Production Management Plus gives you the capability to keep customers advised about their order status. It improves customer service and keeps customer satisfaction rates high by allowing your team to maintain accurate expectations.
Optimize Inventory Management. This software’s integrated inventory management controls allow your team to lower the risks of errors from exporting spreadsheet data, sales order data, or when manually creating purchase orders to ensure materials are at levels required to meet customer demand.
Track Complex Costs. Production Management Plus gives you the capability to track costs beyond a bill of materials. It also gives you the ability to track labor costs and other job-related items, such as:
- Direct AP Costs
- Overhead
- Status
You can get a full picture of costs at any point. Production Management Plus gives you accurate, real-time reports. You can track costs relative to budget and make adjustments to inventory, processes, or materials, as necessary.
Tie Work Orders to Sales Orders. Create work tickets for procurement types that aren’t make to order. Match the order type to the work ticket status.
Automated AP and AR Payments. Scanco Payments delivers a secure, digital, cloud-based payment method for paying suppliers. Available to any Sage customer, it eliminates the time and inconvenience of paying by paper checks. Easily manage your vendor B2B vendor payments and pay them faster using any of the following methods:
- ACH Plus
- eChecks
- Virtual Payment Cards
Scanco Payments streamlines your AR process and frees up time for your Accounting Department by making it easier for customers to pay invoices. They will have the option of paying your sales representatives using Scanco Mobile Sales or using a Click2Pay payment portal on your website. Customers who choose to pay through your website will make their payment using a stored card.
The system is integrated with Sage 100, which eliminates any additional data entry. It ensures that all invoices and customer payments are up to date.
Would you like to learn more about supply chain resilience and how to achieve it for your business? Are you interested in learning more about Scanco Production Management Plus or the other solutions we can offer to assist you with your supply chain concerns? Contact us online or call (330) 645-9959 to make an appointment with a Scanco Solutions Expert today.