March 5th 2025 10:26:27 AM
How to Manage Change and Risk in WMS Upgrades
February 20th 2024 11:00:00 AM
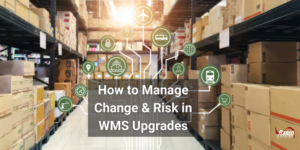
In a previous blog post, we looked at 5 Signs you Need to Update your WMS Solution. This post is for business owners and managers who have decided to upgrade their WMS (Warehouse Management System). It will focus on the steps involved in implementing warehouse management system upgrades and the challenges to avoid when doing the same.
Doing Homework is Essential
The homework stage is when the company looks at its current situation. What elements are working well, and what advantage does the company hope to gain by upgrading the WMS? To get a complete picture, consider the following:
- Compatibility
- Cost
- Functional Capabilities
- Reliability
- Scalability
- Solution Security
- Support
- Vendor’s Reputation
Compare options and choose the one that is the WMS upgrade representing the best match to the company’s budget and requirements.
Anticipate Challenges When Upgrading the WMS
Some team members may initially be off board with the WMS upgrade. The project manager and their team must be prepared to anticipate challenges to the upgrade to persuade the naysayers that this project is best for the company.
- Timing
Why is the WMS upgrade necessary for the company now? Can it wait? Be prepared to explain why now is the best time to schedule the upgrade to the system.
- Features
What new features will the company get from the upgrade the WMS doesn’t currently have? Suppose the existing WMS is out of date. In that case, it may not have the latest features to boost productivity or vendor compliance.
- Complaints About Existing System
Ask the warehouse team for feedback about the existing system, especially what kinds of issues make them frustrated about using it. These comments are constructive when someone in the company doubts the WMS update.
- Cut-Off Date for Technical Support
It is vital to determine whether/when your WMS manufacturer will decide the software is obsolete and stop supporting it. If that cut-off date is coming soon, it is a great reason to upgrade the system.
Get Team and Stakeholders Involved
Suppose a company is going to manage a WMS upgrade successfully. In that case, it will need its stakeholders and team on board with the change.
- Communicate early and clearly that the change is being contemplated.
- Lead with the benefits for all parties, such as the warehouse team members, the IT department, and management. Suppliers and customers should be on the list too. Remember that everyone’s favorite station is WIIFM (“What’s In It For Me”). Getting them on board is much easier if team members and stakeholders can appreciate how updating the WMS will improve things for them.
- Assign roles and responsibilities to all parties. Inform everyone that appropriate training and support will be provided throughout the process.
- Ask stakeholders for feedback. The team members who use the WMS most closely are in the best position to advise management about the features they would like to see in the upgrade. This step goes a long way toward ensuring team members cooperate during implementation.
Manage the Multiple Aspects of the Implementation Process
Implementing a WMS upgrade or enhancement is the most critical phase of the entire project. It includes organizational, technical, and operational components, including:
- Change management
- Data migration
- Deployment
- Integration
- System configuration
- Testing
The company must follow a detailed and highly structured project plan to ensure success. The project manager must track its progress and performance.
At the same time, the project manager must coordinate each implementation stage with the vendor, team members, and stakeholders. The project manager must keep them informed about the project’s status.
Evaluate Results After Deployment
The project will continue once the WMS upgrade or enhancement has been successfully deployed. Evaluating the project’s results and how it benefits everyone is crucial.
The project manager must measure the impact and the project outcomes on the following:
- Business performance
- Customer satisfaction
- Warehouse operations
The project manager and team must compare the “before and after” data for inventory accuracy, costs, quality, productivity, and order fulfillment. The project manager and their team must also take the time to conduct surveys to collect feedback from the warehouse team, suppliers, and customers. They will evaluate the results to determine whether the project was successful. The results are also helpful to indicate any areas where further improvement is needed.
Maintain the WMS
After the WMS upgrade or enhancement is launched, it’s not the time for the team to sit back and congratulate themselves on their success. The WMS is a critical system crucial to the company’s success and must be maintained and optimized. The WMS must be kept running smoothly and continue to meet the company’s needs.
The IT team must perform regular WMS maintenance, updates, audits, and backups (if the company runs an in-house version). The team must also review and optimize the WMS settings, processes, and workflows. It’s crucial to ensure that the WMS version the company is running will provide maximum performance.
Scanco WMS Professional Handles the Most Complex Operations
If your company wants to update to the most advanced Sage 100 warehouse management solution, Scanco WMS Professional (WMS Professional) is your choice! WMS Professional allows your team to manage pallets and pallet-on-pallet activities and transfers quickly and efficiently from any mobile device. The employees record changes and updates, which are recorded directly into Sage 100.
WMS Professional comes equipped with Scanco Dashboard. This impressive BI tool gives your team insights into fulfilling orders more quickly than ever.
Your company has the utmost flexibility in hardware accessory options for scanning barcodes, looking up items, and sending counts into Sage in real time.
Would you like to learn more about Scanco WMS Professional for your WMS upgrade? Contact us online or call (330) 645-9959 to make an appointment with a Scanco Solutions Expert today. We can help you find the right solution for your company.