March 5th 2025 10:26:27 AM
How Scanco’s Warehouse Automation for Sage Minimizes Fallout from Product Recalls
December 4th 2024 15:30:40 PM
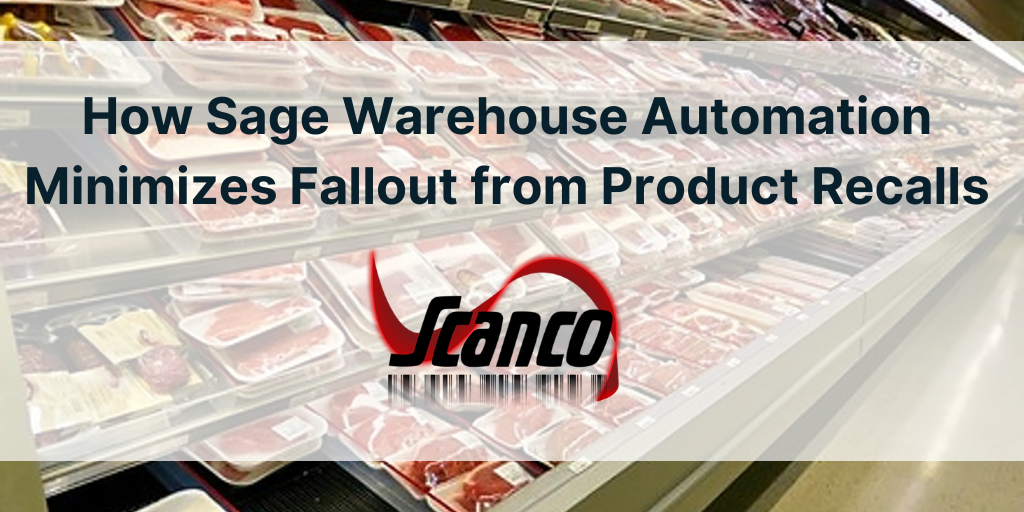
Running an efficient manufacturing, warehouse or distribution operation is challenging enough even when everything goes as planned. However, when a product recall occurs, ‘everything as planned’ goes out of the window.
A product recall — a public call initiated by a manufacturer for the return of a product from the marketplace after the discovery of product defects, contaminations, or safety issues that may endanger the consumer — or put the manufacturer or distributor at risk for legal action — come with extensive headaches and additional corrective costs. The expenses for executing the recalled product, replacing it for consumers who’d purchased it, destroying the recalled supply, the threat of financial responsibility (legal or otherwise) for any recall-related instance, and the publicity hit can, in some cases, amount to hundreds of millions of dollars. The potential cost associated with a recall can quickly turn catastrophic if it goes undetected before it bleeds into distributors, retailers and consumers. For perspective, here’s a short list of a few of the largest food-related recalls in recent U.S. history:
- Peanut Corporation of America issued a 2008 nationwide recall due to a salmonella outbreak caused by longstanding poor sanitation practices. The outbreak eventually encompassed over 3,900 different products, and led to 700 illnesses and nine deaths. The recall’s financial toll surpassed $1B and led to PCA’s bankruptcy, as well as criminal charges for the company’s executives.
- Also in 2008, Hallmark/Westland Meat Packing Company recalled over 143 million pounds of raw and frozen beef products, born from a combination of food safety lapses that led to processing and distributing products deemed unsafe for consumption. It’s considered the largest meat recall in U.S. history, and led to a $497M False Claims Act judgment against the company, which shut its operations shortly thereafter.
- Hillandale Farms suffered from a recall of over a half-billion fresh eggs in 2010. Although this case also resulted in two executive convictions and a $7M fine, Hillandale remains in business.
- In 2011, Cargill Meat Solutions Corporation was the focus of a recall of more than 36 million pounds of salmonella-tainted ground turkey after 90 reported illnesses and one death. The affected plant shut down for a week, reopening only when the contamination source had been identified and corrected — prompting a smaller recall than anticipated.
Food recalls alone involve significant quantities and dollars. According to the Food Safety and Inspection Service of the U.S. Department of Agriculture (USDA), 65 recalls in 2023 involved more than 4 million pounds of recalled product — more than double the reported 2022 total, and four times the total in 2018 — with 2/3rds of the recalled amount a result of processing deviations. Food manufacturing plants, supply chains, and warehousing & distribution have grown exponentially more complex in the last two decades, creating more steps in materials inventory, processing, packaging, outgoing inventory and shipping….with demands to speed up each of these facets to augment profits. With these increased complexities comes increased potential for contamination if every single process isn’t carried out to the letter of the law.
As we’ve detailed, food recalls can cause severe illnesses, loss of life, and significant spending, and can cripple a company to the point of closure. But did you know that a fully automated and compliant warehouse allows you to locate the source of the problem much more quickly, thus minimizing the impact of a product recall? Allow us to enlighten you!
Automation Increases Resilience Against Recalls
Automating incoming raw materials inventory procedures, quality assurance processes, and outgoing finished product inventory helps you know exactly where everything is at all times. Automating processes provides real-time warehouse data from every corner of your operation, which leads to valuable insights and takeaways to help form best practices — what to do, or what not to do, next time to hit your goals. The benefits of warehouse automation also extend beyond your walls; you can track and develop meaningful metrics for your suppliers while materials are in their possession — which enables you to generate qualitative supplier ratings and offer guidance to suppliers when they encounter similar issues.
Traceability is the Key
Once a compromise in raw materials is confirmed, the foremost objective is to identify and isolate the source of the contaminant(s). Only then can you move on to salvaging raw materials and finished products not affected by a breach, and are therefore safe to consume.
In an un-automated manufacturing or distribution operation, it’s likely that the precise location of a raw materials batch could wind up untraceable, as its point-to-point travel may not have been documented at every step since its introduction into the plant. Other important information that may not be tracked: an account of exactly which materials went into which finished products. For example, if only one batch of grain among the ten used to produce a cereal was contaminated, how would you identify which batches of finished product contain the affected grain? Not having the visibility to isolate the locations of contaminated raw material, as well as the locations of finished product containing that material, means that your entire product output — even the non-contaminated part — may be held accountable for only a small portion needing a recall.
A trusted Enterprise Resource Planning (ERP) system provides maximum traceability capacity to quickly identify affected lots in case of a recall. Scanco’s Sage 100 Manufacturing Automation software lets you make the right decisions the first time with the confidence and speed necessary to keep your operations ahead of the game. Sage 100 connects every aspect of warehouse inventory, production, quality control, and automation of job functions to gain insights from real-time data — and keep missteps to a minimum.
Sage Production Management is integrated with Sage 100 software, giving manufacturers and distributors the tools to achieve end-to-end visibility throughout the process. Features including real-time progress reports, inventory management optimization, and configuration with Scanco mobile apps mean increased efficiency from anywhere in the world….and fewer errors in your warehouse. Easily identify the lots and batches that contain the raw materials in question, link those lots and batches to locate the appropriate finished goods, maintain batch integrity, and recall only what needs to be recalled.
Sage Operations Management is a comprehensive solution for automating job management functions for manufacturing, distribution and field service organizations. Operations Management works hand-in-hand with Sage 100 to provide an integrated solution that includes plant operations, financial capacities and automated data in a single source. Sensible use of warehouse automation technology can help minimize the consequences of a recall — and even prevent one from occurring. If any unusual or unauthorized activity is detected, your warehouse operations staff can gain immediate insight into the issue and respond appropriately to hasten negative impact. Furthermore, Sage 100 can detect anomalies in equipment, access and data manipulation that could lead to contamination.
Scanco’s solutions are compatible with the Food and Drug Administration’s final rule on Requirements for Additional Traceability Records for Certain Foods (AKA the Food Traceability Final Rule), which is slated for a January 2026 compliance date that requires entities to share information with other partners in their supply chain. This rule helps push tracking accountability back onto the supply chain by requiring accurate and timely feedback throughout the process.
Staying on Top of Lot Control, Expiration Dates and Shelf Life
There are several things to consider in your manufacturing or distribution warehouse when a product recall occurs:
- How well-tracked is your inventory?
- Have you utilized unique lot numbers to quickly identify and find precise batches of raw materials or finished products?
- Are all in-house materials or finished products accurately labeled with specific production run and expiration dates?
A robust lot control system is critical for dealing with the chaos created by a product recall. Knowing exactly where everything is and being able to monitor and manage inventory based on exact lot location versus an overall quantity in-house is compulsory — especially if your inventory is coming from (or going to) multiple manufacturers or distributors. Additionally, staying on top of expiration dates and shelf life requirements is imperative for maximizing allocations and minimizing waste (remember: different destinations have different shelf life requirements). For example: if the production of ground chicken on Day 10 in a processing plant was compromised and the finished product was shipped to retail stores with a set shelf life of 20 days, documented step-by-step lot control could significantly limit your projected loss of recalled product.
Scanco’s Sage 100 Multi-Bin solution, used by more than 600 manufacturers and distributors, enables the tracking of specific items in multiple bin locations. Fully integrated with Sage Production Management and Sage Operations Management and designed exclusively for Sage 100, Sage 100 Multi-Bin can increase warehouse efficiency by up to 75% with features such as real-time inventory allocations that track from receipt to shipping, directed picking, directed put away, and more. Sage 100 Multi-Bin makes lot enhancement a breeze, and allows you to easily streamline your operation when working with multiple manufacturers or distributors. Sage 100 Multi-Bin tracks detailed expiration dates and shelf life to meet any industry requirements, so you can find the product you’re looking for right away.
When a product recall arises, ensure you have the best resources working for you when you need them the most. Contact us online or call (330) 645-9959 today to make an appointment with a Scanco Solutions Expert and ensure that your manufacturing, distribution, warehouse or supply chain operation is ready to meet even the most daunting challenges with optimal real-time visibility from Sage!