March 5th 2025 10:26:27 AM
5 Strategies for Building Supply Chain Resilience in 2023
February 21st 2023 11:00:00 AM
The supply slowdown businesses experienced in the early part of this decade has forced companies to look at supply chain resilience more carefully. Rather than trying to predict whether the next disruption will be due to another round of COVID, a new war breaking out somewhere in the world, or a natural disaster, business owners would be much better off spending their time building resilience into their supply chain to protect it from threat.
Supply Chain Slowdowns in the 2000s Have Had Multiple Causes
The global pandemic was only one reason for the supply chain slowdown businesses dealt with over the past few years. Other factors contributed to the issue, including the following:
- COVID Pandemic
People became ill with COVID, which made them unable to work. The fear of contracting COVID meant employers had to institute physical distancing policies, and fewer employees could work in physical spaces in offices, stores, and warehouses. Productivity suffered as a result.
- Russian Invasion of Ukraine
The conflict has led to a price jump for several commodities, including oil and gas, food products, and fertilizers. The supply chain disruptions have increased freight charges and created a shortage of shipping containers. Several ports have been closed, and multiple orders have been canceled due to shipping delays and congestion.
- Semiconductor Shortage
The global semiconductor shortage is due to demand exceeding capacity. It will take some time to resolve since there is a long lag between the time manufacturers determine more capacity is needed and the time they can produce more products to meet that demand.
- Extreme Weather
Hot, dry weather led to the Rhine River in Europe water levels dropping, leading to a significant disruption in Germany’s water freight. The River typically moves 80% of the country’s water freight; water levels in places that generally measure 10-15 feet are too shallow at only five feet to allow large vessels through.
Impact of Supply Chain Disruptions
According to McKinsey, supply chain disruptions cost the average organization 45% of a year’s profits over ten years. Is there a better reason to take charge of this issue and manage risk starting today?
Strategies for Building Supply Chain Resilience
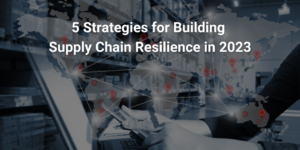
It’s impossible to be prepared for every eventuality when it comes to supply chain resilience. There are too many unknowns. However, one thing for sure is that supply chain resilience requires flexibility, cross-channel transparency, and preparedness. The following strategies will help achieve those goals:
1. Build flexibility in the supply chain.
Plan for multiple eventualities before they happen. These plans could include holding onto extra inventory, working with several suppliers, hiring additional workers, or establishing a relationship with a temporary agency that can supply workers when needed.
Consider the costs of each of these plans, choose simple projects, and avoid ones that will result in high overhead costs. If any plans adopted as a temporary measure interfere with the company’s overall efficiency, look for ways to make the operation leaner.
2. Add new suppliers to the manufacturing network.
It’s always a good idea to have new and backup suppliers that can be counted on to deliver raw materials and finished products available. Suppose a company is too dependent on a single source. In that case, it will suffer the consequences if that supplier can’t deliver on time (or at all).
Working with multiple suppliers can lead to more competition and better pricing and payment terms for materials and finished goods.
3. Look for suppliers located geographically closer.
When suppliers are closer to the companies they serve, they can deliver quickly. The company can save on delivery fees and benefit from greater inventory control.
4. Create inventory buffers.
Buffers are expensive, but they can be a savvy move if the company invests in extra stock wisely. When launching a new product that is expected to move quickly and sell well, it may make sense to stock up on additional capacity to avoid stock-outs. If a particular product has historically sold well during a season, it will likely do well again. Ordering some extra products is also a good idea since there is evidence that it is a good seller.
5. Keep employees informed of disruptive events.
The company’s sales and customer service teams are interacting with customers regularly. They need access to company data so they can respond appropriately to queries about customer orders and when out-of-stock items may be available. These employees will also need guidance about suggesting alternatives to customers who wish to place orders but don’t want to wait.
Automate Your Warehouse Operations to Build Supply Chain Resilience
It’s impossible to anticipate every type of supply chain issue that may impact a business in 2023. Automating warehouse operations goes a long way toward preparing for problems that arise over time.
Scanco offers solutions for businesses of all sizes, from small companies to enterprise-level operations, to keep inventory under control. Our Advanced and Professional Warehouse solutions include the following advanced functionality options:
- Multi-Bin allows users to track one item in multiple bins at once. It is used by over 600 manufacturers and distributors using Sage 100. This option integrates with Work Order, Sage Operations Management, and Sage Production Management.
- Wave & Directed Picking tells team members where to go in the warehouse and allows them to group several orders from a single screen to optimize the picking process using intelligent warehouse mapping.
- Directed Putaway directs warehouse workers to the correct putaway location. It cuts the time they spend walking around the warehouse, searching for the right area.
To discover more about Scanco’s warehouse automation solutions for Sage 100, contact us online or call (330) 645-9959 to make an appointment with a Scanco Solutions Expert today.