March 5th 2025 10:26:27 AM
4 Techniques for Multi-Warehouse Inventory Management
August 23rd 2023 11:00:00 AM
When your business reaches the point where you are storing your inventory in more than one warehouse, consider it a positive sign. It indicates your company has grown beyond the point where one warehouse is sufficient for your needs. As you move to a multi-warehouse inventorysystem, it’s normal to wonder whether you may have expanded too quickly.
There are good reasons for moving to a multi-warehouse inventory plan. Once your business is getting orders from multiple locations, it is a savvy business move to consider storing your inventory in more than one location.
Advantages of Multiple Warehouses
If your company is selling to customers regionally or globally, keeping all the inventory in one warehouse may no longer be viable. It will be more difficult to fill orders promptly and shipping costs may be too expensive for customers to afford comfortably. With multiple warehouses, you can ship from the warehouse closest to the customer’s location. Taking this step also saves on shipping costs.
Challenges Associated with Multiple Warehouses
Operating multiple warehouses offers significant benefits. However, it can also present some issues. Having more than one warehouse complicates your operation. You need to ensure each warehouse is stocked appropriately; inventory must be maintained in each location. Some of the challenges associated with managing several warehouses include:
- More Difficulty with Managing Inventory
Keeping all your warehouses stocked all the time is challenging. Management may end up focused on one warehouse more than others before realizing that the stock and sales aren’t in line. Stock-outs can affect your supply chain and your revenue stream.
- Issues Managing Communication Between Warehouses
Even though you have more than one warehouse, your customers see your business as a single entity. When customers in different regions place orders, it is critical that their orders are communicated to the correct warehouse for delivery.
Miscommunications and errors may take place occasionally, leading to losses. It’s challenging to streamline the processes required from ordering to delivery when your business operates multiple warehouses. Employee errors in ensuring the correct warehouse fills orders may lead to delays or even cancelations.
Techniques for Multi-Warehouse Inventory Management
1. Automate Your Warehouse Management Processes
The most important technique for managing your multi-warehouse inventory is to automate your processes. Cloud-based inventory management systems and warehouse management systems (WMS) are critical tools you can use for this purpose.
Multi-warehouse inventory management software gives you the capability to track inventory levels at different locations in real-time. A cloud-based warehouse management system allows your team to:
- Monitor data in your warehouse from any device.
- Transfer products between warehouses to fill customers’ orders. This practice reduces the likelihood of errors in your inventory.
- Send orders to warehouses with stock available to avoid delays or lost revenue.
2. Optimize the Warehouse Layout
Optimizing the warehouse layout for maximum efficiency can go a long way toward boosting inventory management. A well-organized warehouse directly impacts how quickly customers receive their orders.
Place the most popular items closer to the loading dock so pickers can get to them more efficiently.
Labeling bins and shelves clearly also assists with efficient put-always.
For large warehouses that employ temporary workers, posting a layout of the warehouse in multiple locations is helpful. Taking this step helps them find product bins more quickly.
3. Add Suppliers into Your Inventory Management System
Adding your suppliers into the inventory management system is an effective strategy for keeping inventory to the required levels. Your management team can access information about availability, pricing, and lead time. This information makes the ordering process much more efficient.
4. Track Inventory in all Warehouse Locations
Company business managers should be constantly aware of inventory levels in all warehouses. It’s not practical to take a daily physical count of inventory.
An inventory management system integrated into your multi-warehouse management software makes tracking all inventory quicker and easier. Scanning the inventory as it arrives in the warehouse updates the record automatically in real-time. Once the items are scanned into the system, it’s much easier to confirm stock availability.
Scanco’s Warehouse Automation Solutions Fit Your Multi-Warehouse Needs
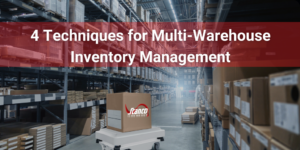
Our warehouse automation tools give your employees exactly what they need to pick, pack, and ship orders efficiently. We base every one of our solutions on meeting your needs.
Scanco WMS Advanced integrates seamlessly with Sage 100 and gives you the automation your multiple warehouses need. This application optimizes and mobilizes your picking and shipping functions. Choose from the following options to customize your solution:
- License Plates/Pallet Transactions
- On the Water
- Wave Batch Picking
Scanco WMS Professional is our most advanced Sage 100 warehouse management solution. It was developed specifically to handle any distribution or warehouse operation needs your company may encounter.
WMS Professional gives you the capability to easily manage pallets, pallet transfers, and pallet activities using your mobile phone. Keep track of your inventory from any location, at your convenience.
This application option is also flexible. Choose the hardware accessories that suit your operation best for maximum effectiveness.
Do you agree with our techniques for multi-warehouse inventory management? To find out more about Scanco’s automation solutions to help you grow your business as you add more warehouses to your operation, Contact us online or call (330) 645-9959 to make an appointment with a Scanco Solutions Expert today.