March 5th 2025 10:26:27 AM
Warehouse Management Tips to Motivate Employees
March 22nd 2023 11:00:00 AM
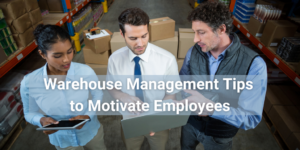
We know that attracting and retaining top-performing employees in the warehouse industry continues to be an issue. Many job seekers still believe that this industry only offers dirty, low-paying work with no real opportunities for advancement. Once your company gets job candidates through the door and brings them on board, how can you encourage them to remain part of your team? Here are some warehouse management tips that can help keep your operation organized and motivate your employees to perform well at work.
Warehouse Management Suggestions to Keep Employees Motivated
- Be transparent with workers.
Employees appreciate it when upper management is honest with them. Suppose they see the company processing many new orders. Still, the employees need to be paid more for their hard work. In that case, the workers will become resentful, and some will (understandably) start to look for work elsewhere. Company executives should take the time to share with warehouse workers how much their efforts are worth and how much the business can afford to pay them. If the employer treats the employees fairly, the employees will be prepared to work hard on the company’s behalf.
- Set employee production goals at the start of the year or each quarter.
Give the warehouse team a set goal. Make it clear that it is a team goal and that everyone has a role in helping the group achieve it. To get the warehouse employees on board, offer an incentive to the entire team if it successfully reaches the production goal.
- Give employees the tools they need to complete their work.
The company hires employees to perform specific warehouse tasks. Managers may ask the employees to perform extra work. The company must ensure that the employees stay energized doing busy work.
Voice picking is a technology that frees employees’ hands to work efficiently. It also helps keep employees motivated at work.
- Allow team members to use scanning systems on their preferred mobile devices.
Give employees some flexibility and allow them to choose a piece of equipment they know. Some warehouse employees may decide to use their cell phones to scan inventory. In contrast, others may wish to use a barcode scanner with a pistol-style grip.
Training time shrinks when employees use scanning systems on the equipment of their choice. It reduces the number of mistakes, and the team members can check inventory more quickly.
- Schedule regular maintenance for all warehouse equipment.
This is a situation where the adage, “If it ain’t broke, don’t fix it,” doesn’t work. Don’t wait for equipment to break down and impact normal warehouse operations. Invest in regularly scheduling maintenance for your equipment. Your company will be much less likely to have a situation where the equipment will break down unexpectedly or run the risk of injuring employees.
- Upgrade to LED lighting in the warehouse.
LED lighting is a cost-effective and energy-efficient choice. LED lights produce less heat than other options, which keeps the warehouse cooler and more comfortable for employees.
- Update your racking system.
Suppose your racking system is modern and organized. In that case, it will help your employees make the most of the available warehouse space. Team members can easily access the most popular (fastest-moving) inventory items.
- Make employee safety training (and refresher sessions) enjoyable.
All warehouse employees should receive regular safety and compliance training. Rather than give the employees a manual or a book to read and decide that the training requirement is finished, find a way to make the training interesting for employees.
Make a short video covering safety training aspects with a multiple-choice quiz at the end. Employees who get a passing score win a small prize for their efforts.
- Make a point of cross-training employees.
When the company introduces a cross-training policy, it helps to ensure that it is prepared if team members become ill or happen to leave. Set aside a certain amount of time quarterly to devote to cross-training. The company will be prepared for staffing shortages, and employees will stay motivated since they have new learning responsibilities.
- Invest in a cloud-based warehouse management system.
Your company can access real-time data when you invest in a cloud-based warehouse management system. Your management team can easily track exactly how much inventory you have in stock at any time. If your company operates multiple warehouse locations, your team can keep on top of all merchandise no matter where it is stored.
Counting inventory is much easier when team members can scan barcodes and the warehouse management system updates the totals in real time. Your buyers can see which items are running low and can place orders for the required items. The warehouse will have fewer stockouts and overstocks.
Scanco Warehouse Automation Gives Your Team Everything It Needs to Process Orders Quickly
Do you need warehouse management software that gives your employees all the tools necessary to pick, pack, and ship orders efficiently? Scanco’s Warehouse Automation solutions are designed for businesses of all sizes, from small to mid-sized to large enterprises.
We can provide your company with solutions to assist your warehouse team with counting inventory and the hardware accessory options to make scanning barcodes quick and efficient. Our solutions use Sage 100 software to record your inventory counts in real-time.
If you need more advanced solutions, Scanco offers WMS Advanced. This option includes everything in the basic model plus Wave Batch Picking, License Plate/Pallet Transactions, and On the Water so your team can pick and ship confidently.
Enterprise-level companies need our most robust solutions. Scanco WMS Professional includes all the features from our Basic and Advanced models plus Scanco Dashboard. You get a BI tool for real-time insights to fill orders even more quickly than before.
To discover more about Scanco’s Warehouse Automation solutions, contact us online or call (330) 645-9959 to make an appointment with a Scanco Solutions Expert today.