March 5th 2025 10:26:27 AM
3 Reasons Your Traditional Supply Chain Design Needs to Be Updated
February 1st 2022 11:00:00 AM
It’s no secret that supply chains have undergone dramatic changes over the past several years. As a result, companies need to adopt fresh, new perspectives to supply chain design. These approaches will shift the emphasis from reducing costs to creating value. The supply chain design process must also respond to the recent volatility and uncertainty in the supply chain due to the Covid-19 pandemic still affecting businesses.
To meet these challenges, your business will rely on modern supply chain software and the expertise of your management team. This approach improves decision-making transparency and reflects the real-world challenges companies face in 2022.
A Changing Supply Chain Environment
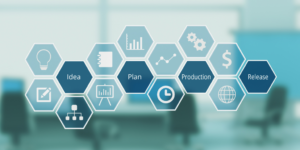
Supply chain design is based on ideas from the 1990s. These studies focused on the supply chain’s physical configuration (facility locations) and customer allotment decisions. Supply chains were designed with lowering costs connected with facilities, warehouses, and transportation in mind.
The supply chain design is usually reviewed from time to time. A company’s major planning decisions are not made based on its results.
This policy is no longer acceptable. During the last 20 years, the business environment has become much more competitive. Now an acronym describes the “new normal” in some parts of the business world: VUCA.
What VUCA Means for Your Business
VUCA stands for volatility, uncertainty, complexity, and ambiguity. According to the Harvard Business Review,
- Volatility is a challenge of something “unexpected or unstable.” The challenge may not necessarily be hard to understand; information about it may not be available.
- Uncertainty means that the basic cause-and-effect for an event is known despite a lack of facts. “Change is possible but not a given.”
- Complexity means that a situation has several parts and variables. Some information is available or reasonably predicted; the nature or volume of the information makes it overwhelming to process.
- Ambiguity means causal relationships are not clear. No previous cases exist, which leaves you completely “in the dark.”
A VUCA environment is the reality for many companies in 2022. As brands embrace multi-sourcing and globalization in a world where economic and political uncertainty is a given, there are constant uncertainties in the supply chain.
When shifting customer expectations are added to the mix, service responsiveness and flexibility have changed how businesses approach supply chain design. Since supply chains represent a significant competitive factor, design has taken on new importance in overall corporate strategy.
3 Reasons Traditional Supply Chain Design Should Be Updated
The way companies do business has changed. Supply chain design needs to be updated too. The following are some reasons why the traditional supply chain design viewpoints no longer work:
1. Keeping the focus on cost reduction is an outdated approach.
The traditional management method used centralized warehouses located in areas selected for low real estate costs. Today, since customers expect to receive goods quickly, warehouse space is chosen based on proximity to the customer base and speed of delivery.
2. Traditional methods can’t capture the complexity of modern supply chains.
Businesses need to invest in updated supply chain software to gain complete visibility throughout their supply chain. Traditional supply chain processes generally don’t include factors like supply chain disruptions, demand uncertainty, and multi-channel distribution. All these factors are common in modern business.
3. Supply chain design must be an ongoing process.
Traditionally, companies conduct a supply chain design review every few years. In modern markets, managers make decisions quickly based on accurate data at hand. Businesses can’t rely on data gathered a few years ago when making decisions for the supply chain today.
Supply Chain Visualization Essential for Making Decisions
There is so much data available to business owners and managers today that there is a real possibility of decision overload leading to decision-making paralysis. Company leaders need data to help them make informed, realistic choices without adding extra “noise” into the mix.
A solution allowing decision-makers to visualize the supply chain in its entirety leads to better decisions. The managers can make informed choices that enable them to focus on customer service, making changes as circumstances change.
Scanco Helps You Mobilize and Automate Your Supply Chain
Scanco’s Sage solutions give you precisely what you need to manage your manufacturing or distribution operation. We work with businesses of all sizes, from start-ups to large enterprise companies.
- Scanco WMS Essentials integrates seamlessly with Sage 100 to eliminate the need for data entry and paper counting. Your team can scan bar codes, look up items, and scan counts in real-time into Sage 100. Scanco WMS Essentials includes Advanced Item Inquiry, Receiving – Receipt of Goods, Inventory Receipts, Quick Picking, and more.
- Scanco WMS Advanced optimizes and mobilizes your picking and shipping. This option also includes Multi-bin-directed order picking, Multi-bin functionality, Proof of Delivery, Inventory Receipts, Inventory Transfers, Alias Item Creation, and Bin Transfers. Run this software option on your iOS, Android, or Windows mobile devices and discover the convenience of its voice command capability.
- Scanco WMS Professional can handle the most complex warehouse and distribution operations. Trust this software option to manage your pallets and pallet transfers, pallet activities using your mobile device. All changes and updates will be uploaded directly to Sage 100. Scanco WMS Professional also includes Scanco Dashboard, which gives you real-time insights to ensure you can fill orders more quickly than ever!
- Sage Production Management gives discrete make-to-stock manufacturers and fabricators complete visibility into their entire production process. This robust software option gives you real-time item statuses, allowing you to keep customers informed about the status of their orders. Manage your customer expectations as you get a complete picture of your operation. Production Management also allows you to easily track all job-related costs relative to budget and make adjustments, as necessary.
Would you like to discover more about Scanco’s supply chain software solutions and how they can benefit your business? Contact us online or call (330) 645-9959 to make an appointment with a Scanco Solutions Expert to take the next step today.