March 5th 2025 10:26:27 AM
Inventory Management in the Food and Beverage Industry
September 6th 2022 11:00:00 AM
The food and beverage industry has weathered the pandemic in reasonably good shape. Production for many companies has remained stable or increased over 2021 levels. Many companies want to expand their current facilities or invest in new equipment. Attracting employees remains a challenge in the industry, with employers offering higher wages and improved benefits to keep qualified workers. Efficient inventory management plays a significant role in ensuring higher profitability and allocating products effectively.
Food Industry Trends and Obstacles
Food Engineering magazine recently published a report discussing the trends and obstacles currently shaping the industry. An overview of the report’s findings is as follows:
- A majority of survey respondents (67%) said that gross throughput grew by an average of 24% in 2022. This rate was two percent higher than in 2021. One-third of respondents stated their gross throughput stayed the same.
- Total cost per product jumped from 11% to 15% per product year-over-year. Over half (52%) of survey respondents reported that their cost per product was higher in 2021, and that number surged to 81% in 2022.
- Forty-two percent of 2021 survey respondents said their cost per product remained stable. In 2022, that number fell to 16%.
- Eighty percent of respondents are considering upgrading their equipment; 21% said this was a “great need.”
- Seventy-eight percent were interested in improving supply chain management; 22% stated this was a “great need,” compared to 11% in 2021.
- Most survey respondents want to expand or retrofit their food processing plants (55%) or packaging lines (55%).
Inventory Management Challenges in the Food and Beverage Industry
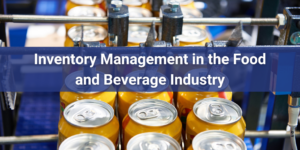
The food and beverage industry is unlike other industries that work with large inventories. Often, the stock includes perishable items. This fact changes the way food companies are required to manage their inventory. Inventory management software can assist with managing the supply chain, delivering products, and helping to ensure customer safety.
- Health-risk issues for the public
Food and beverage companies must always be conscious of their inventory’s “best before” limitations. Since they deal in perishable items, they are always under strict deadlines to promptly move products through their facility, either for production or to a retailer’s shelves.
- Temperature requirements determine warehouse placement
Some food items must be stored in a temperature-controlled environment. Highly perishable foodstuffs can only be placed in specific sections, leaving limited space for dry goods.
- Balancing stock is an ongoing issue
If there is an excess of inventory, then there is a risk of spoilage before it can be used or sold. Too little stock can mean losing business from customers and wholesalers.
Inventory Management Solutions Make Product Monitoring Easier
Some fundamental food and beverage inventory management strategies to consider include:
- Batch and expiry tracking
Tracking is a crucial inventory management technique in the food and beverage industry. Fresh produce and other perishable products are susceptible to spoilage. A company must be ready to recall the affected products if a batch becomes spoiled or contaminated.
Batch and expiry tracking monitor a batch’s movements so that older stock is sold or used first. This First in, First Out (FIFO) strategy minimizes spoilage.
- ABC inventory analysis
Choosing this type of inventory analysis means putting products into categories based on their order of importance. “A” products are the most valuable, and “C” products are worth the least. Under this system, the more popular items get more attention.
- “A” items should break down into about 20% of products, accounting for 70-80% of consumption value.
- “B” items take up about 30% of products. They account for 10-20% of consumption value.
- “C” items are 50% of products, accounting for up to 10% of consumption value.
An ABC analysis for food and beverage companies allows them to focus on the highest value products without keeping excess stock on hand.
- Just-in-time inventory management
This inventory management technique originated in Japan due to the country’s lack of natural resources and limited space. Just-in-time (JIT) is currently used by many food and beverage industry businesses since finished products typically have a short lifespan. This method can help keep inventory costs down and minimize loss.
Scanco WMS Advanced: Your Fully Automated Inventory Management Solution
Scanco WMS Advanced gives you high-level automation that integrates seamlessly with Sage 100. Multiple hardware accessory options are available. Your team members can use barcode scanning to make your distribution process more efficient and cost-effective.
When you choose Scanco’s warehouse solutions, you receive advanced options as part of your package.
Multi-Bin allows your team to track one item in several locations in the warehouse.
Wave & Directed Picking means paper pick tickets will become a thing of the past. Your team members can save steps by grouping multiple orders and saving time.
Directed Putaway instantlypoints your team to the correct putaway location for all items.
Do you Ship Items of Varying Weights? Catch Weight Makes It Easy
Catch Weight is an optional add-on module to Scanco’s Sage 100 Warehouse automation solution. Developed to meet the needs of specialty food manufacturers and vendors who sell products by the case or other units of measure, Catch Weight allows your company to bill customers for your products by the pound. This option also allows you to automate vendor lot traceability and manage expiration dates to allocate products more effectively. With Catch Weight, your team can track shelf-life requirements by the customer and break up the picking order by region or product type: refrigerated, frozen, or dry goods for maximum efficiency.
Would you like to learn more about Catch Weight? Watch our recorded webinar!
Do you have questions about Scanco WMS Advanced and how it can fit into your operation? No problem! Contact us online or call (330) 645-9959 to make an appointment with a Scanco Solutions Expert today.