March 5th 2025 10:26:27 AM
Manufacturers Shifting to Make-to-Order Due to Supply Chain Disruptions and Consumer Demands
October 5th 2021 11:00:00 AM
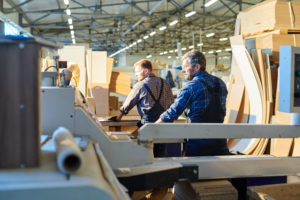
Supply Chain Stressors Pre-Date COVID
It’s easy to blame the global pandemic for all the issues affecting the global supply chain. While COVID-19 does play a role, the problems started before anyone had ever heard of the virus. The trade relationship between the United States and China became stressed when the Trump Administration introduced sanctions and tariffs on Chinese companies. Beijing retaliated in kind, focusing on U.S. agriculture exporters. Companies on both sides stockpiled inventory to avoid paying duties, placing stressors on logistics globally.
Then the pandemic started. The demand for many goods dropped significantly. Manufacturers reduced their capacity during lockdowns. Many workers lost their jobs.
The U.S. started importing again in the summer of 2020. Consumers were ordering online. E-commerce was booming. By the end of the year, issues in the supply chain were becoming apparent.
There is a worldwide shortage of shipping containers. The available ones are costly. Currently, shippers are paying close to $6,000 for a standard 40-foot container. This figure has more than doubled since 2016.
Seasonal Demand Drives Customization in the Food Industry
Certain products may be in demand during certain seasons. As an example, hot dog and ice cream novelty sales spike during the summer. As we move into the fall and winter months, seasonal candies, jams, jellies, pies, and fruit cakes appear on store shelves.
Candies are a product that sells throughout the year. Specialty candy products are produced to tie into Christmas, Easter, and Halloween. Consumers have come to associate these holidays with certain sweet products that may not be available at other times during the year.
Seasonal demand extends into packaging customization. Consumers may be looking to purchase similar products in single-use, family packs, and bulk formats. Their level of popularity may vary, depending on the time of year.
MTO Approach and Optimizing Manufacturing Costs
Why move to an MTO production strategy? For manufacturers, carrying inventory is like keeping spent funds in the warehouse. Perishable inventory means taking a chance on spoilage if orders slow down.
Shifting to an MTO production strategy takes careful planning and more changeovers in the facility. If you are thinking of switching to made-to-order or increasing your MTO processing, let’s take a closer look at what is involved.
Operating your manufacturing business on a make-to-stock basis has the advantage of being more predictable. There is a specific level of inventory to fill. The production schedule runs on that basis.
An MTO production fluctuates based on customer demand. There will be more frequent changeovers required to produce various SKUs as needed. Ideally, you want to make your changeovers as streamlined as possible to minimize disruption to your production efficiency.
How to Keep Your Make-to-Order Facility Working Efficiently
The following are some suggestions to keep your MTO-driven facility working efficiently while dealing with multiple disruptions.
1. Ensure departments are communicating with each other.
Clear communication between departments is necessary for a successful make-to-order production strategy. For example, the maintenance team knows that a changeover takes two hours. The scheduler has allotted only half that time for the task. Production will not run on schedule unless both departments can get on the same page about the actual time needed.
Frequent changeovers mean your team needs to be even more diligent about tracking your equipment’s performance. This job requires more oversight than a checklist can provide. The data needs real-time updates to ensure teams are coordinating information and parts are available when needed.
2. Ask employees to share their ideas for improvement.
Manufacturing floor and warehouse workers are a great source of information about increasing efficiency.
- Set up a virtual suggestion box for employees to share their ideas with management.
- Conduct employee surveys to ask for input.
- Encourage workers to connect with management via email or chat directly to discuss their ideas.
The employees closest to the process can often suggest minor changes that will make the system more efficient.
3. Minimize downtime during changeovers.
Ideally, you want to have either a processing or a packaging line running when your facility is operational. A way to accomplish this goal is to schedule your packaging lines to start during production. The packaging lines can continue when the production line has stopped for cleaning. When packaging is complete, you can start running the next SKU.
4. Set up a preventive maintenance schedule.
Don’t just keep your equipment running until there is a problem. Schedule preventive maintenance checks before you have to deal with an equipment breakdown. At that point, you have no control over when the downtime happens.
5. Use inventory management software to track raw materials.
Shifting to a make-to-order approach means the way your business sources its raw materials also changes. It no longer makes sense to carry a large amount of stock in storage waiting for customers to place orders. Instead, your business will need to pivot its ordering to a just-in-time delivery schedule. Ideally, your facility will receive raw materials shortly before they are needed. The goal is to minimize the time they sit in your warehouse.
Scanco Production Management Solutions Help Your Business Maximize Efficiency
Scanco has manufacturing automation solutions for businesses of all sizes, from small and medium-sized companies to enterprise operations. We know that each manufacturer has its unique challenges trying to get quality products to customers on time. Scanco also knows that automation is the key to increasing productivity and boosting your bottom line.
Contact us online or call (330) 645-9959 to make an appointment with a Scanco Solutions Expert to take the next step now.