March 5th 2025 10:26:27 AM
The Top Operations Management Issues Facing Medical Device Manufacturers in 2022
May 17th 2022 11:00:00 AM
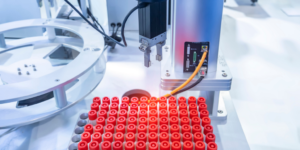
Before the worldwide COVID-19 pandemic, the United States medical device industry was healthy, with an estimated market share of USD 176.7 billion (2020). The sector held its own during the pandemic and saw a slight growth of about five percent. (Grand View Research estimates the industry will grow at five percent annually to 2028.)
Challenges for Medical Device Manufacturers in 2022
As the pandemic lessens its grip on the world, medical device manufacturers see their industry move closer to its pre-COVID state. It doesn’t mean that medical device manufacturers are experiencing a year of entirely smooth sailing in 2022. Several issues present operations management challenges for the industry.
1. Supply Chain Issues
Demand for some types of products, such as those used during elective surgical procedures, has fallen during the pandemic. During the pandemic, orders for products like masks, gloves, infrared thermometers, PPE kits, and testing kits surged.
The coronavirus has caused disruptions to supply chains across multiple industries, and medical device manufacturing is no exception. Companies have been experiencing problems with rising costs of materials and delivery delays. Until the global supply chain issues resolve, the market will continue to experience difficulties with interruptions and fluctuations in supply pricing.
2. Inventory Uncertainty
Supply chain issues and inventory uncertainty go hand in hand. Over the past couple years, we have seen how the pandemic has impacted the supply chain. Other factors can also hurt supply, such as labor unrest, armed conflict, natural disasters, transportation issues, and unexpected increased demand for raw materials.
3. Complicated Manufacturing Standards and Regulations
Several manufacturing standards and regulations applicable to medical device manufacturers include the following:
- ISO 13485
This quality management system is designed for medical device manufacturers. Companies compliant with ISO13485 have improved risk management, quality control, traceability, and process validation. Manufacturers that remain compliant will find it easier to access international markets. Compliance can streamline your company’s processes and make your company more efficient, risk-averse, and profitable.
- 21 CFR 820
The Code of Federal Regulations Title 21, Section 820 is a quality system regulation. It includes requirements for the methods used in manufacturing facilities for designing, manufacturing, purchasing, labeling, and storing medical devices. The regulation also applies to how medical devices should be installed and serviced. The Food and Drug Administration (FDA) inspects manufacturing facilities to comply with this regulation.
- EU Medical Device Regulation
In May 2021, new European regulations on medical devices took effect (European Union Medical Device Regulation). From that point, manufacturers focused on retaining approval “throughout a product’s lifecycle” instead of obtaining post-production approval.
Specific devices are now re-classified under higher-risk classes, and manufacturers must adopt stricter standards. Packaging for European-bound devices includes information in the national language, and the European Union has 23 official languages. Manufacturers must take on the responsibility and expense of providing the necessary information in the appropriate languages depending on their shipments’ destination.
4. Skilled Worker Shortage
The difficulty of attracting employees is a significant challenge for many industries. Manufacturers are having a tough time finding the workers they need to fill open positions.
According to Industry Week, the lack of workers doesn’t stem from the Baby Boomer generation retiring or from workers leaving their jobs because of concerns they might contract COVID-19. If these reasons were contributing to the issue, the workforce’s average age would be dropping significantly. Instead, the average age dipped slightly to 42.2 years old in 2021 from 42.5 years old in 2020.
Employees who left their jobs cited wanting more flexibility and a better work-life balance as their decision. They also stated they wanted opportunities to work from home when possible.
Operations Management for Sage 100 Helps You Address Top Issues
These top issues facing medical device manufacturers add extra challenges to doing business in 2022. That doesn’t mean you and your team can’t successfully overcome them. When you choose advanced operations management software for your company, you are well-positioned to respond to situations as they present themselves. You aren’t running around putting out fires after the fact or expending energy anticipating problems that may or may not happen.
- Operations Management for Sage 100 gives your team the capability to manage purchases by tracking start dates for each job phase. The software will create materials lists and purchase orders so you don’t get stuck with too much inventory or don’t have enough materials to start a job.
- The Sales Order Module of Operations Management eliminates data entry by generating a work ticket automatically. This module will convert an approved, detailed quote to a sales order with a single click. Your sales team can confirm materials availability before committing to a completion and delivery date, which helps solve any inventory uncertainty issues.
- Operations Management also allows you to generate detailed cost estimates for a customer, including materials, labor, and any subcontracted services. Reuse past quotes for the same customer by copying the software’s existing templates to save time and money.
- Use mobile barcode scanning to track products to ensure compliance. This method is much faster and more reliable than attempting to perform these tasks manually. Use Manufacturing 100 barcode scanning to track your status updates, finished good entries, and timecards in real-time.
- Operations Management for Sage 100 gives you more precise scheduling and time tracking for jobs. Once you can schedule labor and time for job runs more accurately, the next step could be to address offering more flexible scheduling for employees. It is worth discussing with employees to get their ideas about “better work/life balance.”
These are the steps that make for a happier, more productive workforce, which is something that will ultimately benefit your company.
Warehouse & Shipping Efficiency for the Medical Device & Pharmaceutical Industries
Contact Scanco to Learn More About Operations Management for Sage 100
Would you like to take the next step and learn more about Operations Management for Sage 100? Contact us online or call (330) 645-9959 to make an appointment with a Scanco Solutions Expert to take the next step today.