March 5th 2025 10:26:27 AM
Scanco Partner Spotlight: Kerr Consulting
September 10th 2024 08:19:05 AM
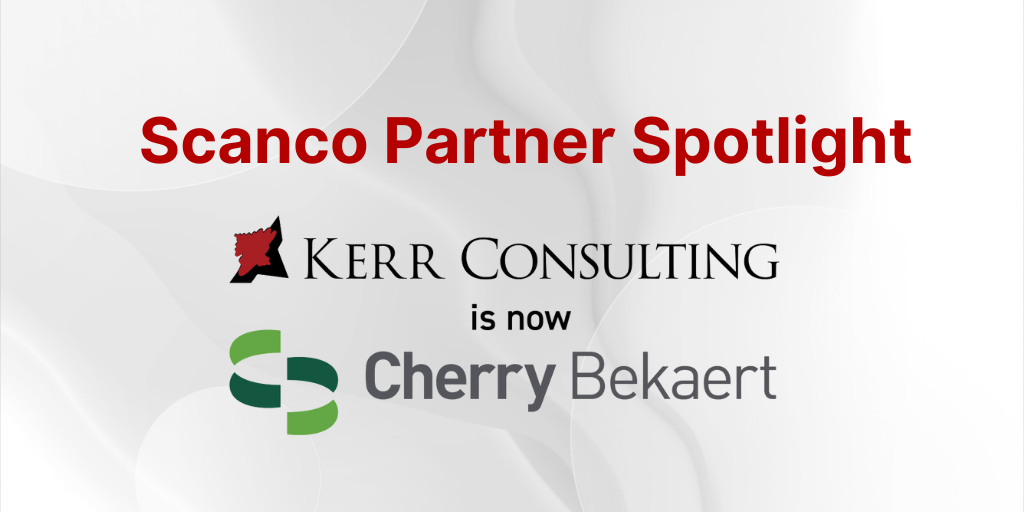
Kerr Consulting is a premiere technology solutions provider through automation, integration, and development. Their digital transformation strategies have allowed thousands of companies to focus more on their core business. In July 2024, Kerr Consulting joined forces with Cherry Bekaert, combining leading business applications and cloud technology solutions with expert advisory, assurance, and tax services. This partnership offers clients a more comprehensive suite of services, delivering a truly holistic approach to business transformation for companies of all types.
Kerr operates as an end to end managed services administrator, specializing in business applications and cloud technology. Offering world class solutions to small, medium, and enterprise customers, and solving their business challenges by designing innovative technology strategies that drive success.
How does the strategic partnership between Kerr Consulting and Scanco bolster client expansion and growth?
“The combination of Kerr Consulting and Scanco can drive significant additional value to clients getting the “best of the best”. Kerr knows Sage software, with 1000s of manufacturing clients across all of the products and has integrated Sanco products with a large percentage of these; Scanco’s experience developing and deploying manufacturing specific solutions is second to none. The combination means that we have seen and successfully addressed the challenges that manufacturers have experienced many times, individually, and can leverage that experience and expertise together to create even more value to manufacturing customers.“
Could you please provide us with some information about your company’s background and what you specialize in?
“Kerr is one of the original Sage VARs, founded in 1987. We have 8,500 clients+ across all 50 states and 26 countries. Kerr is 100% Sage dedicated – as we believe in focus, and to that end Manufacturing is one of the industries we are focused on.”
As a consultant, what tips and tricks would you think are valuable to others in the manufacturing and warehouse industry?
Understand Your WMS Features Thoroughly
- Training & Documentation: Ensure all users are properly trained in the system’s capabilities and understand the available features. WMS systems often have underutilized tools that can optimize processes. With Scanco’s on-demand LMS, users can continue to learn, fine-tune existing skills, and get the most use out of their system.
- Customization: Leverage system customization for workflows specific to your warehouse (e.g., pick-and-pack operations or multi-warehouse management).
Optimize Inventory Accuracy
- Cycle Counting: Implement regular cycle counting processes through your WMS. This helps keep inventory records accurate and avoids costly errors.
- Barcode/RFID Integration: Use barcoding and/or RFID technology for faster, more accurate tracking of items and reducing manual errors.
- Real-Time Updates: Ensure that your WMS is set to update inventory in real time. This prevents overstocking, understocking, and stock discrepancies.
Utilize Location Management Features
- Dynamic Location Assignment: Take advantage of dynamic locations for products with irregular movement patterns to maximize space and reduce picking times. Scanco’s MultiBin product line compliments your Sage 100 ERP by building off-base functionality that allows users to move and track goods seamlessly in and outside of your warehouse.
Pick Path Optimization
- Wave or Batch Picking: For high-volume picking, use wave or batch picking strategies that the WMS can automate to reduce unnecessary travel and improve pick times.
- Zone Picking: If your warehouse is large, consider using zone picking to divide picking responsibilities by areas, allowing for more efficient task management.
Leverage Data Analytics
- KPIs and Dashboards: Use the built-in analytics of your WMS to track Key Performance Indicators (KPIs) such as pick rate, inventory turnover, and order accuracy.
- Historical Data for Forecasting: Analyze historical data to forecast future demands, allowing for better stock management and staffing decisions.
- Labor Management: Some WMS solutions offer labor tracking. Monitoring the performance of your workforce can help with scheduling and operational improvements.
Automation and Integration
- ERP Integration: Integrate your WMS with Enterprise Resource Planning (ERP) systems for end-to-end visibility of the supply chain. This can streamline procurement, production, and fulfillment processes.
- Automated Replenishment: Set up automated replenishment triggers when stock levels hit a certain threshold to ensure seamless production or order fulfillment.
Improve Receiving Efficiency
- Pre-Receiving Notification: Enable Advanced Shipping Notice (ASN) integration, allowing your WMS to prepare receiving areas and staff for incoming shipments. With Scanco’s SPS Commerce integration, users can leverage ASN labels directly from a handheld scanner.
Simplify Returns Management
- Automated Returns Process: Use the WMS’s return management module to streamline reverse logistics, creating easy workflows for returns, inspections, restocking, or disposal.
- Labeling for Returns: Automate returns with clear labeling and disposition codes so returned items are easily processed.
Mobile Technology
- Handheld Devices: Use mobile devices (scanners, tablets) integrated with your WMS to perform tasks like picking, cycle counting, and inventory checks, providing mobility and real-time updates.
- Voice-Activated Picking: Consider implementing voice-activated picking systems to free workers’ hands and increase accuracy in picking operations.
Continuous Process Improvement
- Routine Audits: Periodically review WMS usage to identify bottlenecks, inefficiencies, and errors, then adjust workflows or system settings accordingly.
- Feedback Loop: Encourage employees to provide feedback on WMS processes and use their input to tweak or refine the system for smoother operation.
Compliance and Safety
- Compliance Tracking: Use your WMS to maintain compliance with industry standards, regulatory requirements, and safety protocols by automating tracking and documentation.
- Safety Alerts and Warnings: Set up your WMS to trigger safety warnings for hazardous materials handling or when inventory levels reach dangerous thresholds.
By utilizing these tips and tricks, businesses can increase operational efficiency, reduce errors, and improve overall warehouse performance. Regularly revisiting your WMS setup and staying updated with new features or integrations is key to long-term success.