March 5th 2025 10:26:27 AM
Warehouse Automation Lowers Risk of Workplace Injuries
August 2nd 2022 11:00:00 AM
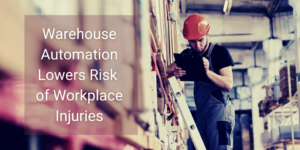
According to the U.S. Bureau of Labor Statistics, there is good news on the employment front in the transportation and warehouse sector. It added more than 600,000 jobs between February 2020 and March 2022.
This industry saw employment grow by 10.5%. The growth in jobs is due to consumers predominantly working and staying at home while turning to online shopping.
As a warehouse owner or manager, you want to keep your facility running smoothly. If you have reached the point where it is (for the most part) fully staffed, don’t overlook taking steps to keep your employees safe while on the job. Warehouse automation has a role to play here.
- You are probably ensuring the floors are clean and dealing with spills promptly to avoid slip-and-fall injuries.
- There is a First Aid kit on the premises in case of an accident.
- You have an eye wash station installed if your facility handles harmful chemicals.
- Your team has received safety training and attends follow-up sessions regularly.
Workplace Injuries Mean Days Away from Work
In 2020, there were 24,900 incidents where warehousing and storage workers were injured and had to take time off work to recover. Most of these injuries (12,220) involved sprains, strains, or tears, and approximately 1,500 cases were fractures (U.S. Bureau of Labor Statistics).
While an employee is off work recovering from an injury, the rest of your team is affected. They may need to work harder to make up for the lost employee. Morale may suffer in the group due to work-related injuries. Other employees may have concerns for their health because of this event.
Warehouse Automation Maintains Safety and Increases Efficiency
Your human resources are the most valuable assets your business has at its disposal. Business machines, computers, and even robotics have their place in a modern warehouse. Still, even the most sophisticated piece of equipment can’t operate entirely independently.
1. Automation allows team members to focus on more satisfying work.
Warehouse space is at a premium, and many facilities use every inch of space available, including in the vertical plane. The higher items are stacked, the more difficult it becomes to pick them for orders, and the more team members are required to get a thing down. Automated forklifts are a much better and safer plan than expecting employees to climb ladders to retrieve products stored on high shelves or bins. Employees are always in danger of losing their balance and falling, especially if the product is heavy or awkward to carry.
Reassign employees to tasks requiring judgment and decision making where that team member can provide more value to the company. The job will likely be more exciting and satisfying, improving your company’s retention rate.
2. It lowers the risk of injury from repetitive motions and physical strains.
Ergonomic concerns in the workplace include the following:
- Awkward postures
- Heavy lifting
- Overexertion
- Repetitive motion
- Strain
- Undue physical stress
Any of the preceding can lead to the inability to work, chronic pain, and time off for the injured employee. Production slows down, and you, as the employer, will incur additional costs.
Introducing solutions like barcode scanners makes inventory management much quicker and easier for team members. They spend much less time counting inventory, and you can access the scanned results in real-time.
3. Automated processes reduce fatigue and support productivity.
Distributors have been under pressure to keep up with customer demands for the past couple years. They have also been closely monitoring their competition to avoid falling behind. This push to do more and get it done faster has done more than trickled down to the warehouse floor, and it has tumbled down like a waterfall. Employees have borne the brunt of increased demands, and they are tired.
When faced with these challenges, it is tempting for team members to cut back on breaks or skip them altogether. That would be a mistake. Tired employees are more likely to become distracted and make errors on the job. Team members should be encouraged to take regular breaks before they become overly tired to avoid this situation.
Scanco’s Warehouse Automation Solutions Make Sense for Your Business
If you want to introduce warehouse automation to your business, Scanco has the automation solutions to help your company increase productivity while keeping safety a priority.
Our Sage barcode scanning hardware options include models with large-capacity batteries, extended range, and the functionality to perform well in low temperatures. The ZEBRA TC21/TC26 is a good option if you want a barcode scanner in multiple configurations. Use it with a pistol grip or an optional wrist-mounted accessory for hands-free use. This model is suitable for small and large companies.
The ZEBRA MC3300x is a rugged unit with a fit-for-purpose ergonomic design. Its extended range scanning option allows your team members to capture top-rack barcodes. It is equipped with a 35% larger-capacity battery that lasts up to three shifts. The MC3300x’s rugged specs add up to increased reliability and improved productivity on the warehouse floor.
Sage 100 Warehouse means you can throw away the clipboard and automate your warehouse operations. The Wave and Directed Picking feature mean your team no longer has to guess where to find items in the warehouse. It reduces the number of daily steps, reducing wear and tear on their feet, knees, and hip joints. The software allows you to group multiple orders to optimize the picking process, reducing employee fatigue and enabling you to deploy your team members more efficiently.
To learn more about Scanco warehouse automation solutions for your business, contact us online or call (330) 645-9959 to make an appointment with a Scanco Solutions Expert to take the next step today.